Liquid Section
Sugar Syrup Manufacturing Plant

Hygienic manufacturing of liquid syrups in range from 50 Ltrs to
20,000 Ltrs. minimum manual handling of liquids means
maintenance of hygienic process, Quality components in the
plant including Sugar melting vessel, Transfer pumps, Inline
homogenizer and we also provides in them optimum performance
support Pants recognized for delivering outstanding performance
support as well as higher production capacity
Making a cGMP stand./contact parts made of SS316 metal
User friendly design makes it easy to assemble and clean.
Direct transfer of sugar from stores to sugar syrup vessel.
Entry of propeller agitations provided from bottom using
specially designed mechanical seal face.
Controls: Manual ballvalves or automatic pneumatic valves.
Heating Media: Steam or Electrical.
Control panel: Semi Automatic or PLC/ HMI Based.
Model: cGMP.
Storage And Jacketed Tanks
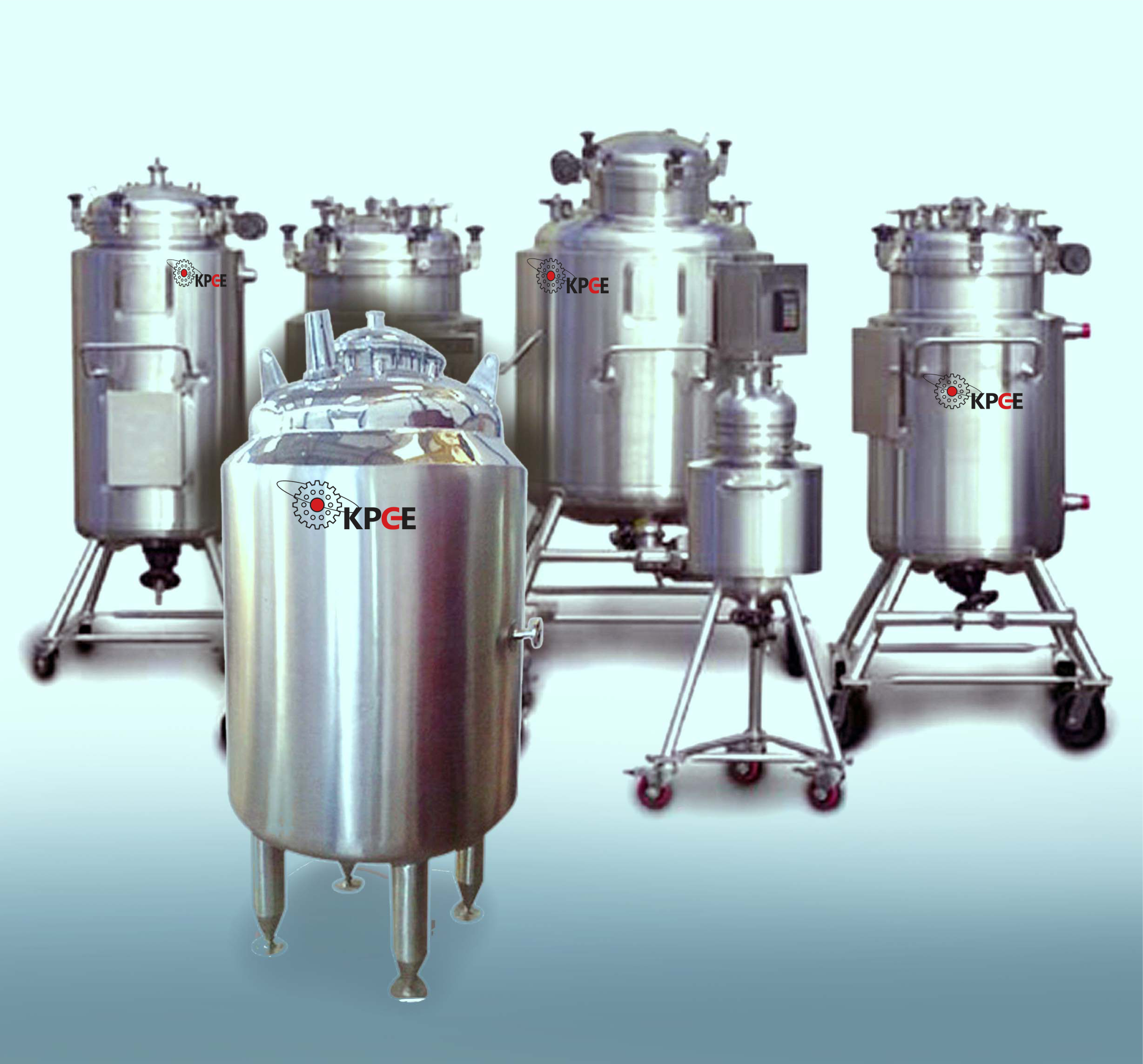
MOC: SS 304 / 316
Agitator: Propeller, Hydrofoil, cowl etc
Capacity: 5 Liters to 30000 Liters
Heating Media: Stea or Electrical
Valves: Ball valves, Flush bottom ball valve
and butterfly valve etc.
Applications
Storage Tanks and Jacketed Vessels are used to manufacture
or store high quality liquids and solutions required by different
industries like Pharmaceuticals, Chemical and Cosmetics etc.
It can be provided either jacketed or non-jacketed versions.
It can be also available in electric and steam heated versions.
The storage tanks and jacketed vessels can be designed in
different rage like, 100, LTR TO 25000 ltrs in any shape and
size as per client’s requirements.
Colloidal Mill
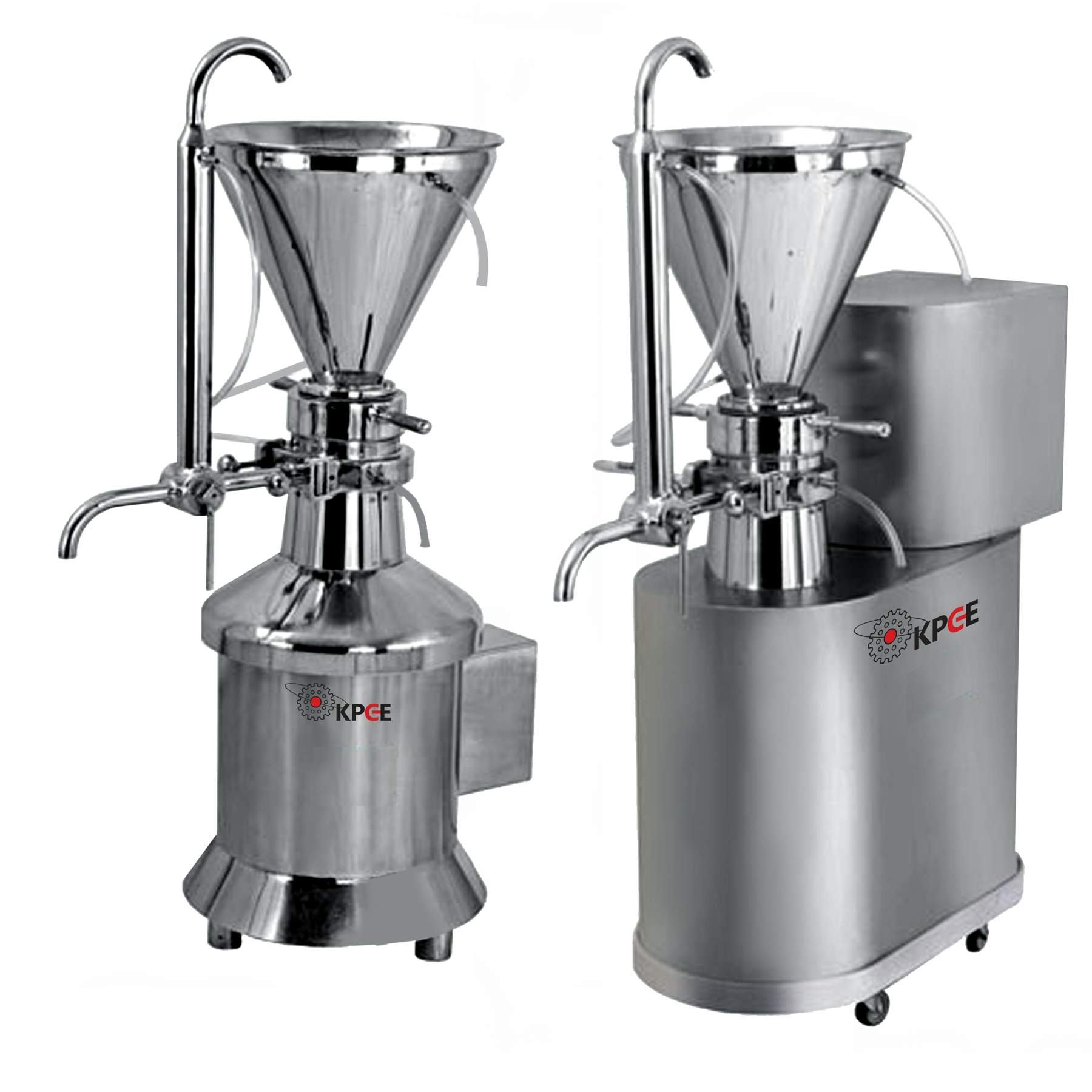
A machine that is used to reduce the particle
size of a solid in suspension in a liquid, or to reduce the
droplet size of a liquid suspended in another liquid.
Colloid mills work on the rotor-stator principle: a rotor
turns at high speeds (2000-18000 RPM)
The resulting high levels of hydraulic shear applied to
the process liquid disrupt structures in the fluid.
Colloid mills are frequently used to increase the stability
of suspensions and emulsions., but can also be used to
reduce the particle size of solids in suspensions.
Higher shear rates lead to smaller droplets, down to
approximately which are more resistant to emulsion
separation.
Volumetric Liquid Filling Machine
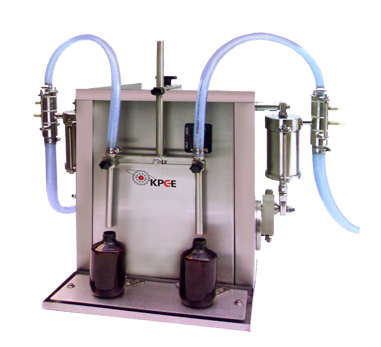
Loader automatically loads empty capsule in the loading plate for
manually operated capsule filling machine, hence it take normally
5 minutes to load empty capsule in 300 holes.
Output: Fill 300 holes plate in 30 seconds give an output of
36,000 (Thirty Six Thousand) capsules per/hour.
Interchangeability: The machine is Manufactured to suit the
following capsule size combination 00/0/1/2/3 or 4/5
Features: Low investment high output significant difference
in your production department easy to operate, can be handled
by semi skilled person, no setting system for any change part.
Technical Specification: Drive ¼ HP 3 phase, 440 volts,
the machine stop automatically after loading is complete.
CAPSULE LOADER
Model: cGMP.
Filter Press / Sparkler Filter Press
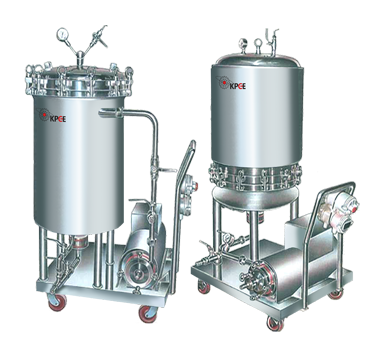
Zero hold up Filter press: Model: cGMP.
Filter press having exactly the opposite direction of flow of liquid
to the flow in standard filter. The unfiltered liquid is fed into
central part of the machine giving high pressure from bottom
inlet. The filter media filters the liquid when the whole liquid
spreads out equally on each plate. Solids remain on filter media
and filtrate liquid collects in the shell, which then comes out
through the outlet. After the completing of filtration process
the cake is cleaned from filter material and can be recycled.
Sparkler filter press: Model: cGMP.
The main operation of is to filter the impure liquid arriving on top
of each horizontal plate with increasing pressure, the filter media
holds back the impurities & allows the filter to pass through center
by interlocking cups, which takes the filtrate to the outlet of the
filter. The cake formed between the horizontal plates can also be
obtained. The function of filtration process becomes slow when
the liquid reached its holding capacity into the cake
Homogenizer
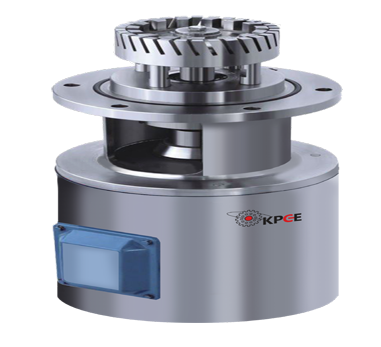
The high pressure homogenizer HPH is an inline dispersing
machine for energy-efficient, continuous production of
superfine emulsions. The dispersing action of the high
pressure homogenizer HPH is not based on the rotor/stator
principle. spontaneous decompression of the liquid from
max. 2000 bar to an ambient pressure. The homogenizers
is recommended when a disintegration down to the nano
range is required; however, these machines do achieve a
smaller flow capacity than conventional dispersers.
The machine's design to fit customer-specific tasks.
The high pressure homogenizer is available in two
sizes with either one or more piston(s) of varying
diameters. These parameters determine the max.
homogenizing pressure (800 or 2000 bar), Feeding
volume (up to 10 ml) as well as homogenizing
results and flow capacities.
Ropp Single Head Cap Filling Machine
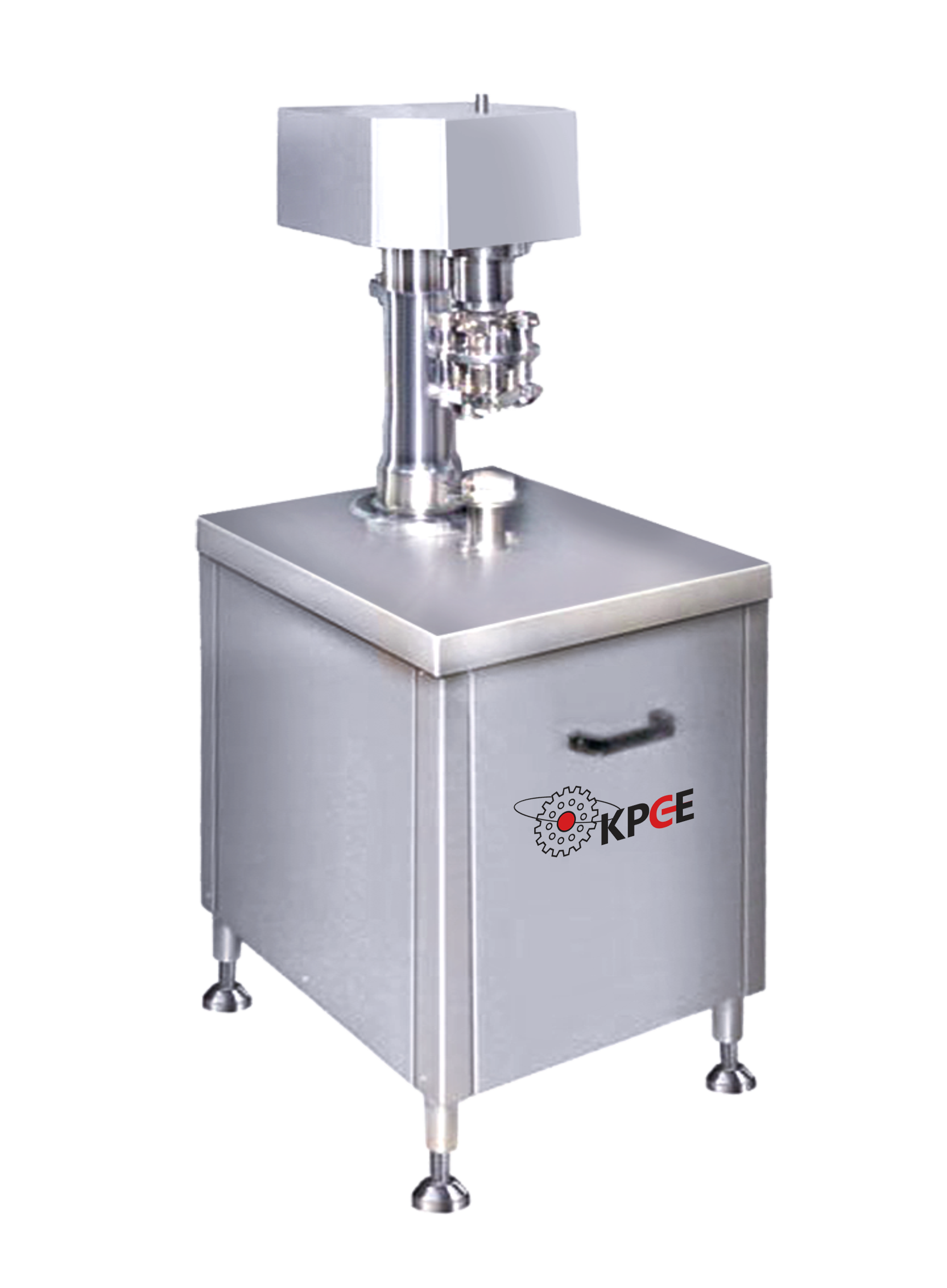
Machine is designed to seal aluminum caps for various sizes
of the bottles fed on a continuous line. Change parts are
available for different size of caps and bottle diameter.
The machine is fully automatic & its operation is very simple.
The bottles are fed by means of a SS Slat conveyor to the
pickup point of cap-vibrater chute a cap is picked up by the
bottle and the star wheel carries the bottle under the sealing
head. The complete head assembly moves down and perfect
closer is achieved by the threading and skirting rollers.
The movement of the bottles is arranged from left to right
on the conveyor.
Model: cGMP. Main drive motor 1.5 HP 415 Volt.
Bottle size tolerance required for the machine & ± / 0.5 mm.
for bottle dia & height. The output cap of machine is 40 to 60
bottles/min. with 'V' Belt pulley drive arrangement.